Measures for Preserving Quality and Safety
Quality policy
"We always satisfy the requests from clients, laws, regulations, and standards, and offer reliable, economical, safe, and worry-free products and services by each deadline."
Our corporate group set the above quality policy based on the ISO9001, a certification for quality assurance management systems, and conducts group-wide activities, including order receipt, design, purchase, production, construction, tests, inspection, after-sales services, and development, with the aim of living up to the trust of clients under the policy of putting importance on clients and satisfying them.
Quality/Environment assurance management
Chart of processes of the quality management system (QMS)
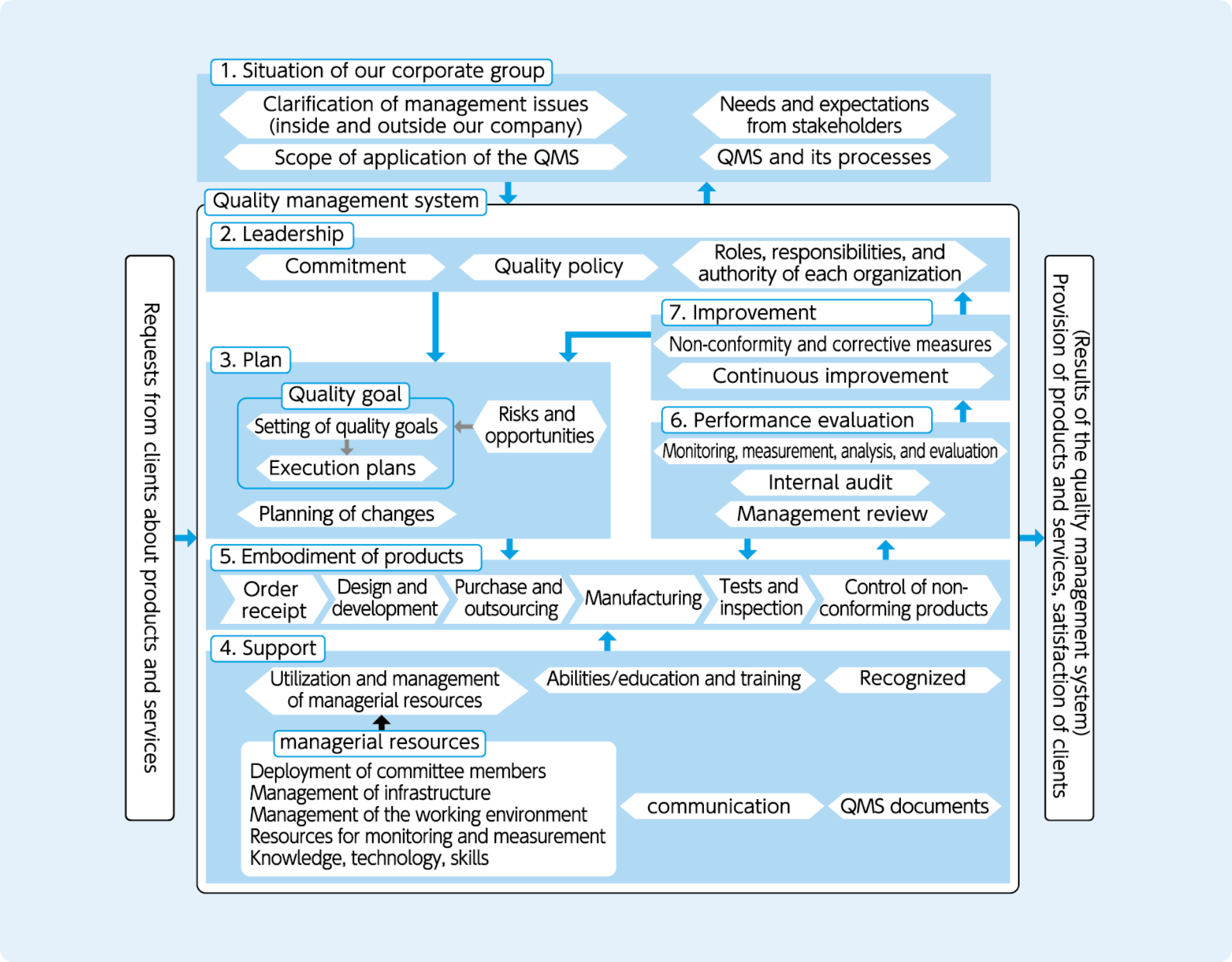
Responsibility
The management systems for quality assurance and the environment of our corporate group are managed by the quality/environment assurance department, which is directly controlled by the president as a secretariat, under the leadership and commitment of the president and the management.
We set group-wide policies for quality and the environment and performance indicators (KPIs) for each fiscal year, and each business division sets KPIs and concrete measures in management programs, with the aim of maximizing our performance. We adopted a system in which the secretariat and quality/environment managers monitor and evaluate our business performance on a quarterly basis. In addition, the president reviews the effectiveness of the quality/environment management systems regularly, and we are responsible for ensuring quality and environmental conservation.
Kakoki Standards
Our company has the Kakoki Standards (KS), which systematically specify necessary items and basic technological items for business execution. The KS is composed of "management standards," "operation standards," and "technological standards." These are reviewed regularly and revised when there emerge some non-conforming products or services, to improve business operations. When the standards are revised, we make the revision known to all employees by utilizing the Intranet, and make it possible to browse the latest version via the Intranet anytime. In our corporate group, the authority to browse the standards was set, to share the standards.
Quality/Environment Committee
For the purpose of promoting quality assurance and environment conservation activities continuously while involving all group companies, we hold a meeting of the Quality/Environment Committee with the president serving as general manager on a quarterly basis, to share the situation with respect to annual KPIs (quality: costs for dealing with non-conformity and the customer satisfaction level, environment: sales from orders related to SDGs and technological development), information on non-conformity, the customer satisfaction level, the evaluation of management programs, etc. and deliberate how to respond to serious complaints about products or services and improve quality. Group companies, too, attend the meeting, to share information and unify our measures.
Analysis and utilization of the results of surveys on customer satisfaction level
After delivering products and equipment, our company surveys customer satisfaction level, and conducts the evaluation and analysis of results. This reflects our intention to improve the quality of products and services to satisfy customers. This also means our initiative for analyzing the reasons why customers chose our company or products and then giving feedback to the product development division and improving the behavior of staff in charge.
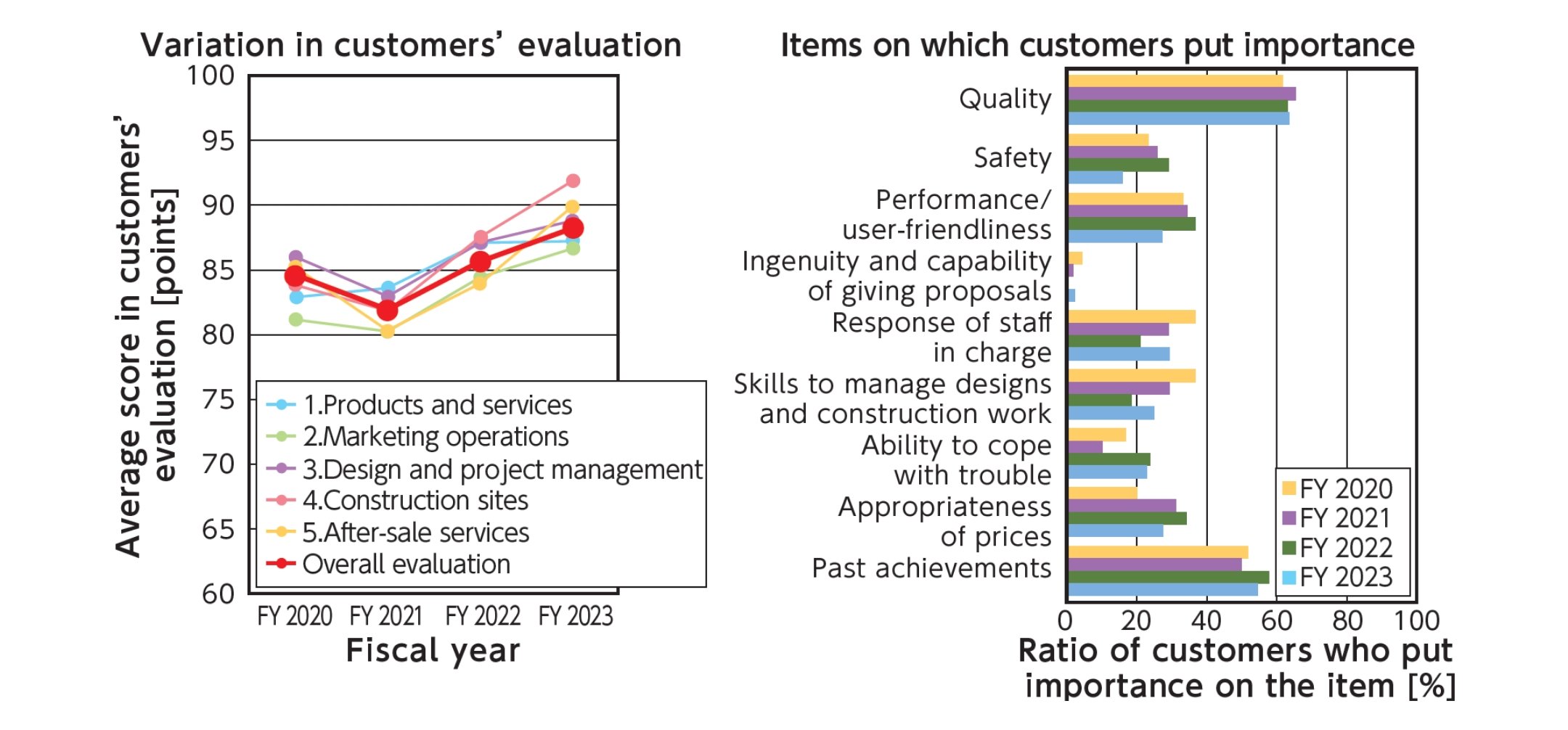
Education of employees about quality
Our company conducts systematic education about the KS and documents for quality/environment management systems. In November, which is the nationwide quality month, we hold an online session about management systems for all employees, contractors, temporary workers, and part-timers, to deepen their understanding of the importance of "observance of rules," "personnel development," "enhancement of verification," and "communication about risks" for fostering the risk-free climate and further enhancing the awareness of quality.
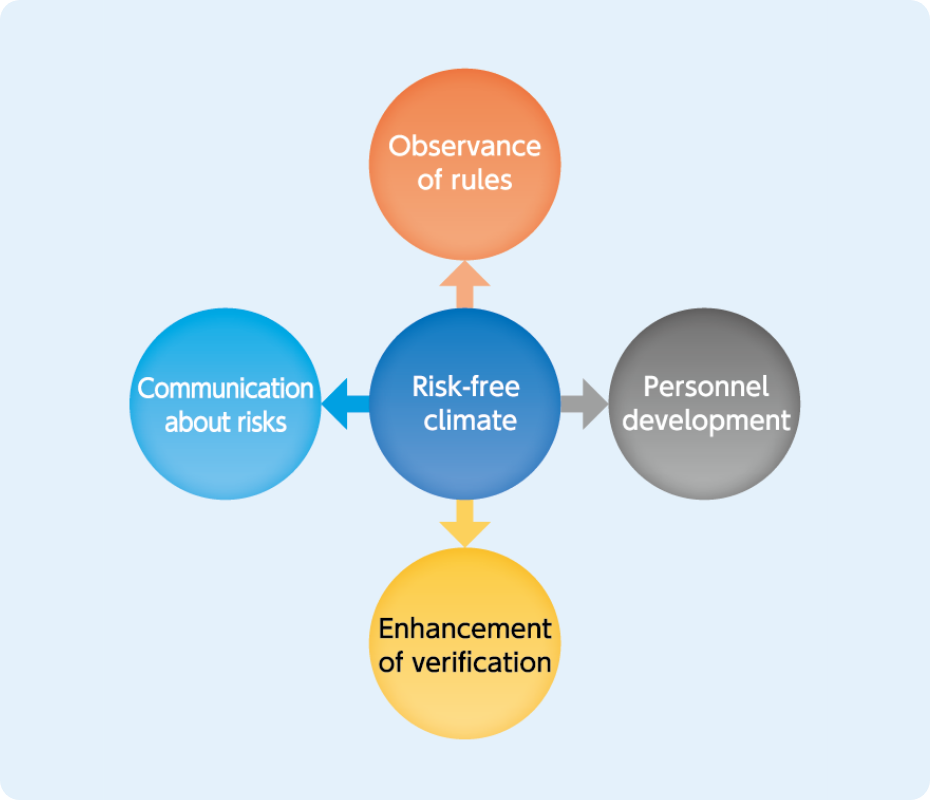
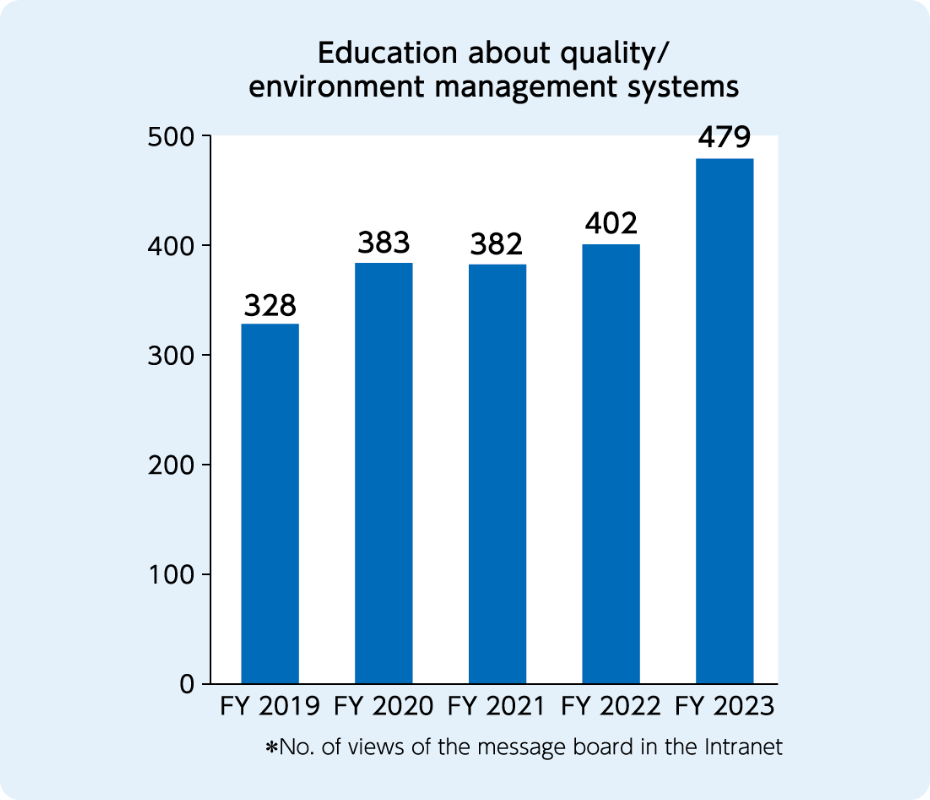
Risk assessment for products
Our company reforms our business portfolio under the management vision. Various risks can be assumed in new business domains and the development of new products.
Our company makes company-wide efforts to reduce and prevent risks through the strategy for rationalization before receiving orders and the management of serious risks based on the control of trial products and changes after receiving orders. In addition, we adopted the phase-gate process in development meetings in 2021. We carry out risk assessment to judge whether or not to release products and evaluate them, and support the realization of the management vision.
Establishment of Safety and Health Management Office
Department of General and Personnel Affairs had managed operations for the safety and health of employees, but in April 2024, Safety and Health Management Office was established, while considering that in order to support our business activities, it is essential to eliminate industrial accidents and develop an environment for the health of all employees of group companies and subcontractors, who work together with us at construction sites.
Code of conduct
To realize a working environment where employees can work safely without worry, and strive to maintain and improve the health of each employee
Major tasks
- Group-wide education on safety for all employees (June every year)
- Holding of meetings regarding safety measures (once a quarter)
- Safety and health patrol by executives
- Efforts to make National Safety Week and Health Week known to al employees
- Items regarding the operation of clinics and occupational health
Examples of our measures
- During Safety and Health Weeks, we encourage employees and their family members to submit slogans and posters about safety, and commend those who have submitted excellent works. Excellent works are displayed in a space around the entrance of Kawasaki Works, and introduced in in-house newsletters, message boards, etc. to attract attention from employees and raise their awareness of safety.
- We hire external intellectuals who are versed in the safety and health of employees, and request them to give technical advice and lectures at the time of in-house training. Like this, we have established a system for complementing our ideas and knowledge, which would fall into a rut if developed internally.
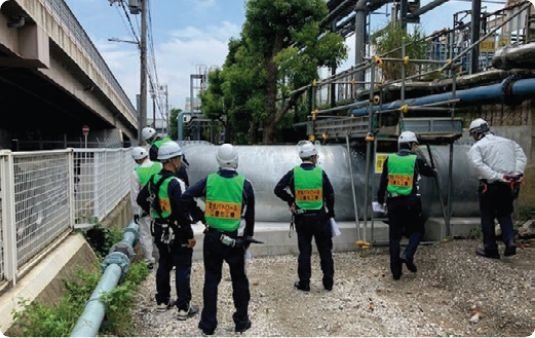
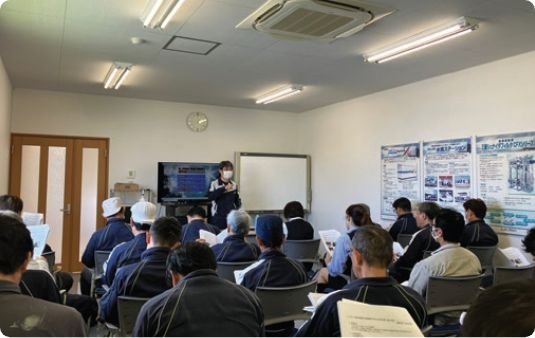